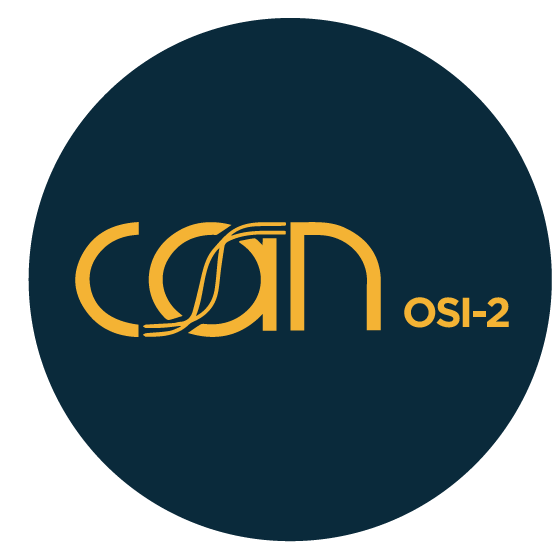
OSI Layer 2
Classic CAN, CAN FD and CAN XL
We offer:
Conformance Tests (ISO 16845-1 and Extensions)
ISO 16845-1 is the standard test specification for the implementation of CAN. This method and abstract test suites verify compliance with ISO 11898-1.
Following the successful update of the CAN protocol to CAN FD, CAN XL is the next step in meeting the increasing demand for bandwidth and cost effective communication protocols. With data rates of up to 20 Mbit/s and data fields of up to 2048 bytes, it closes the gap between CAN FD and 100 Mbit Ethernet (100BASE-T1) and provides the basis for efficient interaction between IP technology and classic signal-based communication.
Even though this seems to be ‘just’ an extension, with the changes it is a new development that needs to be tested as any other developments.
Several CAN XL implementations from different vendors are about to be launched. Car manufacturers are now faced with the challenge of ensuring interoperability in a multi-vendor environment.
C&S has been actively involved in this task from the very beginning. Starting with the specification of the new protocol in the new ISO 11898 Part 1, followed by the definition of the new test cases in the new ISO 16845 Part 2 (Conformance Test Plan), and finally the extension of our test system to include conformance tests for CAN XL. We offer conformance testing for Classic CAN, CAN FD and CAN XL to ensure you are on the safe side when using the new CAN protocol as well as the established CAN protocols.
We take your specific applications and requirements into account when planning and carrying out compliance testing, and support you with our many years of experience. We also offer extensions to the ISO 16845-1 tests, which we have developed based on our experience in conducting tests.
We offer:
CAN robustness tests
The common protocol conformance test is typically based on short test cases that are intentionally designed to verify specific, separated features of the protocol implementation.
In doing so it is neglected, that the behavior in the current state of an implementation, is possibly influenced by the previous states and different conditions.
Therefore our robustness tests check your CAN controller with many successive test cases. Such a robustness test could extend over several days depending on the complexity of your module.
The test cases cover conditions and events that may be critical:
-> verification by pseudo-random data at very high bus load (up to 10,000,000 frames)
-> example of failures occurring in this context: message drop in case of high bus load or transmission blocked
-> example of failures occurring in this context: limitation of message handling and buffer memory bandwidth, partially dropped messages
-> example of failures occurring in this context: transmission blocked, received frame partially dropped
-> the ability to decode valid messages after the bit error has been detected is required
-> example of failures occurring in this context: previous error detection prevents further decoding of valid frames or following frame transmission.
Sections of the test run at very high bus loads are considered in order to create a ‘worst-case scenario’. As a result, errors are created. Different parameters are varied during the test run, such as length and coding of the identifier, length and content of the messages and baud rate.
Our robustness tests can detect problems and sporadic errors which are not detected by the standardized test cases of the ISO 16845-1.
We offer:
CAN Processor Interface Tests
For the different implementations of the CAN protocol it is defined which features they have and how they must behave, which configuration options they provide and which status information they deliver. However the transmit and receive interface to the next layer is product specific.
As a consequence, the amount, size, and handling of the message buffers, the implementation of optional features, power modes and interrupt handling are implemented quite differently.
These product specific properties are described in detail in the datasheet and/or in the manual of the CAN controller.
The standardized test cases of the ISO 16845-1 assume an identical and simplified interface to the so-called Upper Tester (which takes over the functions of the higher layer).
This simplification neglects the impact of the actual processor interface of the behavior of the controller. Therefore as a supplement we offer interface tests to check the specific characteristics of your processor interface in accordance with the device datasheet or manual.
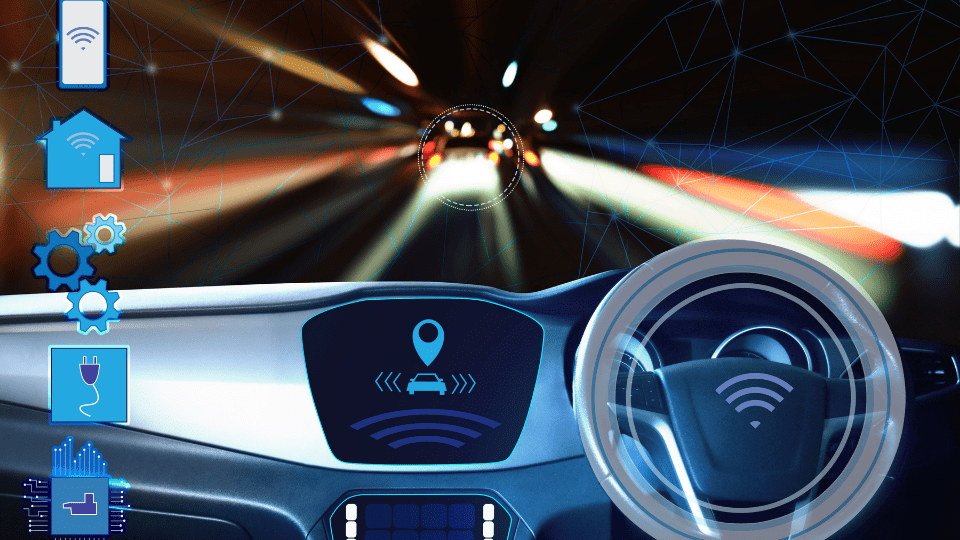
We offer: Testing CAN implementation with extended properties
In addition to the properties defined in the ISO 11898-1, implementation may have other properties that have to be tested. We develop the corresponding test for you.
The principle behind CAN controller tests
Implementation of the CAN protocol has to be compliant with the ISO 11898-1 specification to allow proper communication throughout the CAN network. To verify this conformity, C&S group has developed a test system to execute test cases based on ISO 16845-1 (test specification for CAN implementations).
When performing the standardized conformance tests, we question and evaluate test procedures and test results repeatedly. As a result, it has been determined that the test cases of the ISO 16845-1 are no longer sufficient for many applications. To close this gap and increase the level of test coverage, we have taken into account the development of specific test groups which deal with the processor interface and also with the robustness of the implementation under high and continuous bus traffic.
Our test system was developed based on the architecture defined in ISO / IEC 9646 (standard for conformance testing methodology and framework).
The CAN controller is embedded in a test environment where a so-called Lower Tester takes over the functions of the the OSI layer below the controller and thus handles the ‘bottom’ interface of the CAN implementation.
Accordingly, the Upper Tester takes over the functions of the OSI layer above the CAN controller.
The execution of the tests are controlled by our test controlled software. The data storage of testing results and evaluations are done automatically.
It is also possible to carry out single tests manually while changing the settings of the test procedure. This allows us to react to inconsistencies during test execution and to identify and analyze possible errors in the controller.
C&S publication about CAN/CAN FD data link layer conformance tests
Find below a C&S publication about CAN/CAN FD data link layer conformance test. If you want more information please send us a mail or give us a phone.
At the Automotive Networks 2015, in Munich, our employee Patrick Isensee gave a presentation on November 25, 2015: CAN FD Conformance Testing: Minimum requirement to ensure interoperability